AcousticBioprinting
Established bioprinting processes, such as inkjet or extrusion processes, rely on the use of nozzles, just like the well-known FDM 3D printing techniques. Even though the nozzles are necessary for the printing processes, they limit the process resolution since the only way to increase it when using an optimal parameter configuration is by decreasing the nozzle diameter, changing the machine’s hardware. Smaller nozzle diameters increase the risk of clogging and the shear stress exerted on the bioink, which can in turn lead to irreversible cell damage. The princple of Acoustic Droplet Ejection (ADE) solves these problems by completely avoiding the use of nozzles. In the first phase of the project funded by the German Research Foundation (DFG), we were able to show that cell-laden three-dimensional hydrogel structures can be printed on a millimeter scale using the ADE process. Human mesenchymal stem cells embedded in the single droplets showed a very high viability after the printing process. Using fluid mechanics finite element simulations, we were able to show that the shear stress when printing cells using ADE technology is almost three times lower compared to bioprinting using a microvalve-based inkjet process.
In a second project phase we want to tackle some of the questions the first project phase left unanswered. Based on these questions we devised four fundamental hypotheses for the second project phase: 1.) By avoiding the use of nozzles with the ADE process, bioinks with cell concentrations near physiological levels can be printed. 2.) Using this method, single cells can be printed. This can be achieved by the proper modification of the current hardware. 3.) Even gels with complex gelation techniques can be processed using the ADE process. 4.) The analysis and process control of the behavior of the cell-laden droplets upon impact on the build platform is a basic prerequisite for understanding how three-dimensional cell-laden hydrogel structures can be reproducibly built using ADE technology.
An essential key to testing the working hypotheses in the second phase of the research project is the additional implementation of high-precision 3D measurement technology to the acoustic bioprinting system. This will enable us to monitor the printed objects during the printing process. It will also allow a detailed investigation of the effects of density, velocity, droplet diameter, viscosity and surface tension on the impact of the cell-laden droplets on the building platform and the fusion of the droplets with each other, as well as an analysis of the process-related response of the bio-printed cells. Based on the expected results and new findings from the second project phase, the acoustic bioprinting method can finally be comprehensively scientifically evaluated in direct comparison with established nozzle-based printing processes.
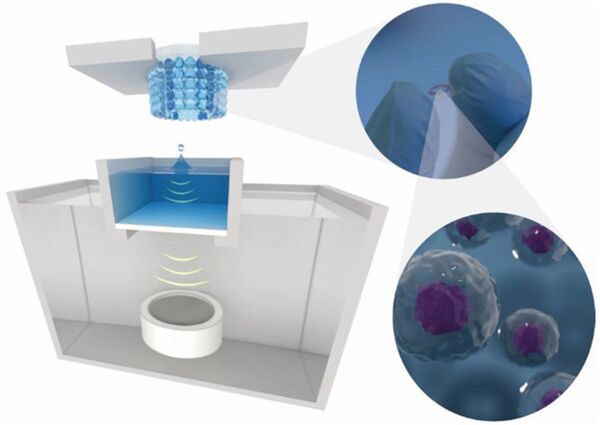
[1] Jentsch S, Nasehi R, Kuckelkorn C, Gundert, B, Aveic S, Fischer H (2021). Multiscale 3D bioprinting by nozzle-free acoustic droplet ejection. Small Methods 5:e2000971. https://doi.org/10.1002/smtd.202000971